完全制御
AIとシームレスなトレーサビリティを備えたマルチカメラシステムにより、不良品が発生する隙を与えません
en.ids-imaging.com
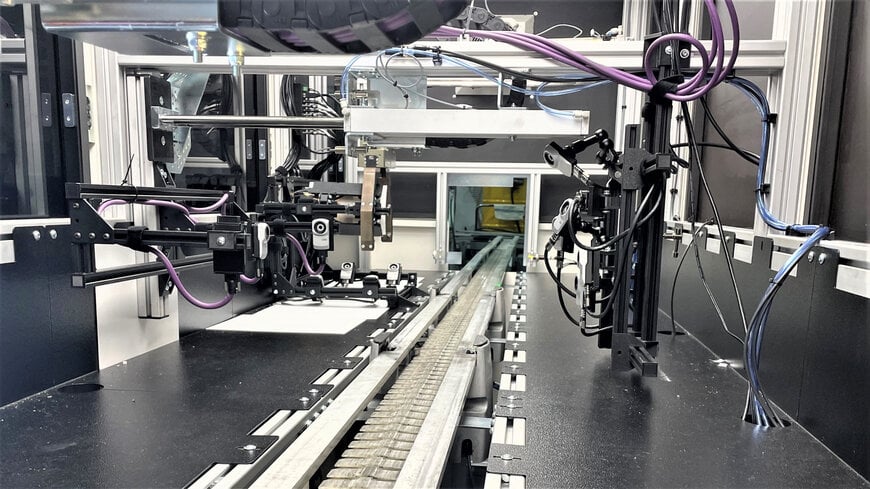
しかし、その要件は高いものです。自動車業界の厳しい品質保証基準を満たすためには、複雑な部品の形状であっても、高い処理速度で検査を行う必要があります。また、最大限の精度と処理の信頼性を確保する必要があります。検出のばらつき、個々のシリアル番号やバッチに対する不十分な追跡可能性、環境条件の変化による問題は、コストのかかるエラー、生産のダウンタイム、クレームにつながる可能性があります。
VIVALDI Digital Solutions GmbHは、AIによるリアルタイム品質検査の実例となる革新ソリューションを開発しました。Intelプロセッサ搭載のエッジサーバーに加え、いわゆるSensorBoxではインテリジェントな画像処理が重要な役割を果たします。自動車部品サプライヤーとそのチェコ共和国の生産拠点向けに設計されたこのシステムでは、最大70台のIDS Imaging Development Systems製USB3.uEye+ XCオートフォーカスカメラが、複数の検査セルで表面検査のための自動視覚検査を行います。
- 強い反射を伴う丸い部品形状も、プロセスの信頼性を確保しながら検査する必要があります
「IDSのカメラが組み込まれたテストセルでは、ドイツのOEMメーカーのアルミニウム部品の表面の高解像度画像を撮影します。今回は電動モーターです」と、Vivaldi社の最高経営責任者(CEO)であるUwe Siegwart氏は述べ、カメラの役割について説明しました。撮影された画像は、露光、ホワイトバランス、色補正などの要因を最適化するために事前処理されます。AIは、傷、気孔、汚れなど、さまざまな表面欠陥を認識します。「チェコ共和国の工場では厳しい要件が課せられています。欠陥カタログによると、0.2ミリメートルの欠陥も確実に検出する必要があります。また、部品1個あたりの検査時間は36秒を超えてはなりません」と、Uwe Siegwart氏は厳しいガイドラインについて説明します。導入が成功したこのシステムでは、1日あたり最大2,400個の電動モーターハウジングが100%自動で検査されます。
- 同時に画像を記録することで完全な検査が保証され、サイクルタイムの維持にも役立ちます
AIのスペシャリストがIDSのuEye XCカメラを選んだ理由は?
「自社開発のカメラコントローラとのインターフェースやコンパクトなサイズに加え、センサーの機能の幅広さ、そしてもちろん必要なカメラの台数による価格も考慮しました」と、Vivaldi社の事業開発部門のEike Humpert氏は語ります。「決め手となったのは、オートフォーカスカメラでカメラから異なる距離にある複数の表面を撮影できることです。これにより、テストプロセスが大幅に簡素化され、効率性と柔軟性が向上します。これは、例えば異なる構成部品のバリエーションをテストする必要がある場合に重要な要素となります。マクロアタッチメントレンズを使用すると、カメラの最短撮影距離も非常に簡単に縮めることができます。
コンパクトなuEye+ XCに搭載されている、onsemiの13.10メガピクセルCMOSセンサーAR1335も、この点で非常に優れています。ローリングシャッターカラーセンサー (4200 x 3120 ピクセル、画素サイズ 1.1µm) は毎秒 20.0 枚の画像を生成し、詳細な画像を保証します。「BSI ピクセル技術により、光の状態が変化しても、センサーは常に正確で信頼性の高い結果を生成できます」と、IDS の 2D カメラ担当プロダクトオーナー、Jürgen Hejna は説明します。このセンサーがこの用途に特に適しているのは、低照度下での優れた性能と最小限のピクセルノイズだけではありません。「24倍のデジタルズーム、自動ホワイトバランス、正確な色補正を組み合わせることで、この厳しいテスト工程の成功に大きく貢献しています」とJürgen Hejnaは強調します。わずか32 x 61 x 19ミリメートルのコンパクトなサイズで、軽量ながら頑丈なこのカメラは、産業用に最適です。さらに、2Dカメラの専門家は、もう一つの利点を挙げています。「このカメラに使用されている部品は、自動車業界向けのソリューションにとって最も重要な要件のひとつである、長期間の入手可能性を特徴としています。」
IDS peak により簡単な導入と最高のパフォーマンスを実現
「USB3.0 経由で IDS カメラの前述の利点を最大限に活用するために、IDS peakを利用しています。IDS が提供する SDK により、IDS Vision 転送プロトコルを当社のコードにシームレスに統合することができました」と、Uwe Siegwart 氏は導入について説明します。IDS の強力なソフトウェア開発キットにより、USB3 Vision 搭載の産業用カメラをこのアプリケーション用に特別にプログラムすることができました。「私たちは、IDS USB3 Vision 転送プロトコル経由で IDS peak を使用して画像を生成する REST API を使用しています。IDS USB3 Vision のおかげで、USB3.0 経由で 5 Gbit/s 以上の帯域幅を利用できます。Video4Linux ドライバーを使用した場合、USB2.0 経由の転送速度は 480 Mbit/s に制限されてしまいます」と、Uwe Siegwart 氏は付け加えます。その結果、帯域幅の増加により、より高い解像度とより短い伝送時間が実現するという利点が生まれます。
- IDS peakインターフェースにより、Vivaldiソフトウェア内でカメラ設定を直接変更することができます
エッジサーバーを介したAIによる分析と同期カメラ制御
同時画像処理タスクは複雑であり、課題も多岐にわたります。アルミニウム部品の表面は光沢があり、光を反射するため、画像に強い影響を与えます。光の反射により、傷、冷間圧延、ビード痕、表面の凹凸などの欠陥が隠れたり歪んだりすることが多いため、これらの反射により、欠陥を確実に認識することが困難になります。さらに、アルミニウム部品の場合、未処理の表面は毎回異なるように見えることがよくあります。加工されていない部分は、異なる構造や色調を示しますが、これらは本物の欠陥と混同すべきではありません。したがって、AIベースの画像処理では、通常の材料構造と、加工対象の表面における実際の未加工部分を正確に区別できなければなりません。
画像処理は、生産ホールの周囲条件によっても難易度が高くなります。特に冷却潤滑剤の混合による空気品質などの要因は、画像の鮮明度やシャープさに影響を及ぼします。さらに、ボックス内の機械や周辺の他の機械による温度変化や振動もあります。これらの振動は画像のぼやけや位置ずれの原因となり、欠陥検出をさらに困難にします。
これらの課題に対応するには、画像処理システムの正確な調整が必要でした。照明、カメラの位置、画像評価アルゴリズムは、反射を最小限に抑え、素材の違いを正確に解釈できるように調整されています。同時に、システムは環境要因による干渉を補償し、常に信頼性の高い結果を出すのに十分な堅牢性を備えています。不良部品は、顧客自信のメンテナンスチームが迅速かつ簡単に交換できるものでなければなりません。
「画像処理は最適化されたインフラストラクチャを介して行われます。USBハブ1つにつき最大8台のカメラを接続でき、複数の検査エリアの同時記録が可能です。これらのUSBハブは最大2つまで、画像信号を束ねて処理する独自開発の「カムコントローラー」に接続されます。複数のカムコントローラーはエッジサーバーにネットワーク接続されています。このサーバーはAI支援分析の計算を行うだけでなく、システムコントローラーと直接通信し、カメラのトリガーを調整して同期記録を保証します。」
最終検査の自動化へのステップ・バイ・ステップ
多くの企業は、AIをサポートする新しいテクノロジーの導入には依然として消極的です。Vivaldiのプロセスは、既存の品質管理を直接置き換えるものではありません。「最初の8~12週間ほどは、従来通りの手作業による最終検査が実施され、当社のvCHECKモジュールがサポートします」とEike Humpert氏は説明します。つまり、最終検査担当者は、集計表や欠陥カードを使って手作業で欠陥を記録するのではなく、個々の(詳細)画像上でデジタルにマーキングするということです。この目的のために、最終制御ステーションにはタッチPC経由のデジタルインターフェースが用意されています。最終検査担当者は画像上で欠陥を見つけ、あらかじめ定義された欠陥カタログに従って分類します。
これには2つの利点があります。まず、最終検査担当者は段階的にデジタルの最終検査段階に導入され、Vivaldiと連携した作業に慣れていきます。次に、エラーのマーキングと分類が施されたラベル付きの製品画像は、AIのトレーニングに使用されます。さらに、過去の不良品として認識された部分など、既存の製品画像もトレーニングに使用されます。これらはクレーム対応の一環として記録されています。
- 「Human-in-the-loop」の実用化 - AI PreCheckは人間によって評価されます
「手動と自動の表面検査を組み合わせることで、大量の画像でもエラー率を1%未満に抑えることができます」と、Eike Humpert氏は強調します。同時に、このアプローチによりAIの継続的なトレーニングが可能になります。ユーザーは、AIによる検査と制御の範囲を常に管理することができます。
常に焦点:トレーサビリティのための情報保存と組み合わせたリアルタイムの画像認識
高性能USB3産業用カメラと組み合わせたCamBoxの導入により、品質保証の面で飛躍的な進歩が達成されました。この技術により、極めて高速なプロセス速度でも、安定した高精度の部材検査が実現します。検出の品質は、変動することなく一定に保たれます。
決定的な利点は、周囲の条件が変化しても信頼性の高い検出が可能であることです。照明や温度、その他の外部要因の変動が検査精度に影響を与えることはありません。同時に複数の検査特性を分析できるため、検査プロセスの効率が大幅に向上します。
- 42台のuEye XCカメラで電動モーターのハウジングを検査
もう一つの優れた特徴は、シリアル番号ごとに画像を自動保存する機能で、これによりプロセスと品質データの完全な追跡可能性が保証されます。つまり、テスト結果はいつでも追跡および記録が可能であり、これは世界で最も要求の厳しい業界の一つにおける品質保証の決定的な要因となります。「最終的な判断は人間が行うべきです」と、Uwe Siegwart氏は言います。「すべてはOEMの厳格な品質保証ガイドラインに適合していなければなりません。各構成部品の完全な付加価値ライフサイクルは、監査に耐えうる方法で文書化される必要があります。つまり、どの部品がいつどのシステムに搭載され、どのテスト機器でどの結果が得られたかということです。」Vivaldiシステムは、これらすべてを保証します。
一目でわかる特長:
• 高速プロセスでも安定したコンポーネント検査
• 変動のない信頼性の高い検出
• 個々の環境条件の変化にも対応する信頼性の高い検知
• 複数の検査特性の同時検査
• 完全なトレーサビリティのための自動画像保存
• 構成部品の容易なメンテナンス
• 構成部品レベルでのトレーサビリティ(プロセスおよび品質データ)
「画像処理はトレーサビリティの中心的な要素であり、ソリューションの技術的な核心部分です。そして、IDSはまさにこの点において理想的なパートナーです。これにより、品質保証とトレーサビリティの輪が完結します」— Vivaldi社CEO、Uwe Siegwart —
- 4セルCamBoxと検査後のワークステーション
「当社の技術は柔軟で、プラットフォームは拡張性があります。最先端のテクノロジーに最適化されており、幅広い製造工程にシームレスに統合できます」と、Uwe Siegwart氏は説明します。「ソリューションの拡張性により、幅広い業界の企業がそれぞれの要件に合わせた品質管理を行うことができます」工程および品質データのインテリジェントなデータ処理により、エラーの原因を早期に認識することができ、製造企業のコアプロセスにおける継続的な工程改善につながります。
「品質データのデジタル化によるリアルタイムでの取得と、他の生産パラメータとのリンクは、効率を高めるだけでなく、不良品や手直し作業を大幅に削減します。エラーは最小限に抑えられ、コストは削減され、生産プロセスは最適化されます。」このシステムはすでにチェコ共和国で成果を上げています。年間クレーム件数は3分の2に減少し、これまで認識できなかった表面欠陥の件数はゼロにまで減少しました。
今後の展望
デジタル品質管理の市場は急速に発展しており、特に高解像度など、より優れたカメラ技術がその要因となっています。「最適化された画像処理プロセスとツールにより、エンドユーザーによるリアルタイム分析も可能になります」と、Eike Humpert氏は述べています。「解像度の向上、よりコンパクトなデザイン、価格最適化されたカメラが求められています。」産業用カメラメーカーであるIDSの製品ラインナップは、最先端の技術でこの需要に応えるように設計されています。
画像の権利 Vivaldi Digital Solutions GmbH
© 2025 IDS Imaging Development Systems GmbH
カメラ
uEye XC - 完璧な画像を自動で撮影
使用されたモデル:U3-36L0XC
カメラファミリー:uEye XC
クライアント
VIVALDI Digital Solutions GmbHは、最新のコンピュータービジョンと機械学習技術を基盤とした、AIによる品質管理のための最先端ソリューションを開発しています。Vivaldiプラットフォームは、すべてのコンポーネントが最高の品質と安全性規格を満たし、表面外観検査における揺るぎない精度と高いプロセス信頼性を保証し、製造プロセスを新たなレベルに引き上げます。