www.engineering-japan.com
03
'18
Written on Modified on
製造業の生産経済学の現状
加工現場では、一定の部品数を一定の品質、時間、コストで生産する方法を模索しています。常に目標を達成するには、切削パラメータ、工具コスト、交換時間、工作機械の稼働率、被削材の取り扱い費用、材料費、人件費など、様々な要素の管理を考慮する必要があります。
生産経済学とは、工程の多数の要素を最適のバランスに維持し、望ましい結果を達成する技術と科学です。2 世紀を超える機械加工の歴史では、生産経済学の要素が増加の一途を辿っています。製造業は、1 品目を生産する手工業から始まり、工作機械を使った標準化された部品の大量生産までに進化しました。製造法の改善により第 2 世代の大量生産が幕を開け、生産ラインで同一の部品を大量に生産できるようになりました。この形態は、少品種大量生産(HVLM)シナリオと呼ばれます。その後、CNC 加工機とロボットの登場により、高効率の第 3 世代大量生産が主流となりました。最近では、プログラミング、加工工具制御、被削材取り扱いシステムにデジタル技術が適用され、Industry 4.0 と呼ばれる第 4 世代の生産方式が登場し、高いコスト効率で、多品種少量(HMLV)生産を実現しています。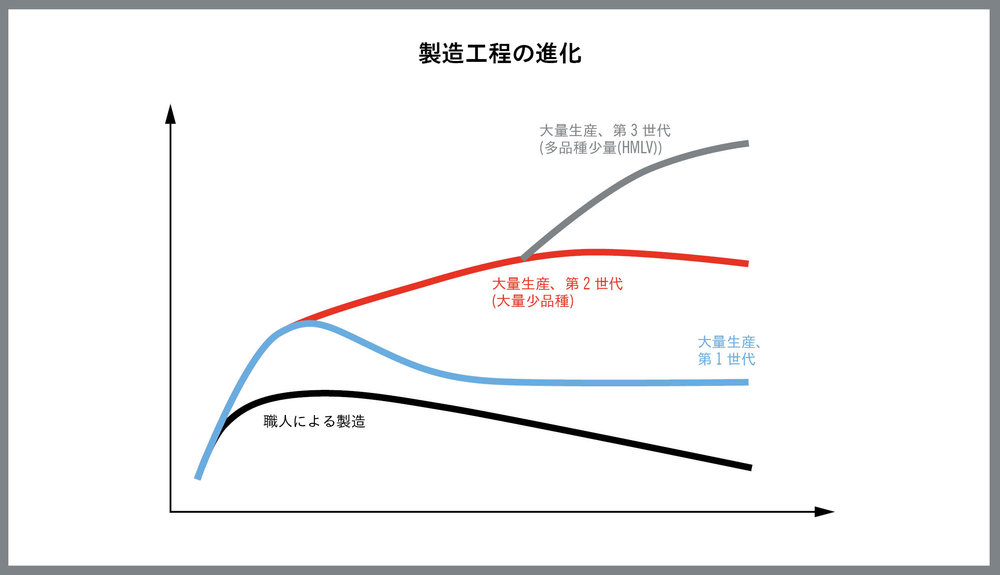
HQ POS Manufacturing Process Evolution.jpg
HVLM から HMLV への生産シフトを効果的に達成するには、製造会社が生産経済学の変化と進展の実情を認識して、運用を分析し、目標を達成するための情報と技術を活用することが重要です。変革で重要なのは、単純すぎる信念と慣行を捨て、生産性を最大限まで高める努力を台無しにしかねない隠れたコストを排除することです。
少品種大量生産のシンプルな経済学とは
標準化された加工工程は、19 世紀に開発され、これにより部品を相互に代替できる同一の製品をすばやく生産できるようになりました。自動車製造業では、この HVLM 生産手法を磨きに磨き上げ、移送ラインや他の手法も確立して、長期にわたって同じ部品を数十万、数百万と生産できる体制を築き上げました。
HVLM 生産には長期間持続する特性があるため、製造業者は多数の工程要素を微調整して、最大の生産量、一貫性、コスト削減を実現できます。また、工具、パレット交換装置、ロボットなどの周辺技術が、製品のばらつきを最小限に抑えます。工程は完璧に稼働し、歩留まり 100 %で、コストを予測可能、不測の非稼働時間、不良品、作業のやり直し、バリ取りなどの二次加工が全くないということが想定されています。
工具コストは、一般的に、総生産コストの約 3 %であるという仮定があります。3 %という数字はベンチマークとしては便利ですが、それが有効であることは稀です。たとえば、被削材種の加工特性は加工コストに大きく影響します。加工材種を鋼からチタンに変更すると、工具使用が 5 倍に増加します。3 %の工具コストは 15 %になり、他の要素も同様に増加します。
工具のエンゲージ時間のみに注目すると、工具交換時の非稼働時間などの他の要因がおろそかになります。その場合、実際の要素が現実からはうまく隠されてしまいます。製造業者は、加工時間、セットアップ時間、工具交換時間、取り付け/取り外し、その他の要因が互いに影響し、阻害することを理解しておく必要があります。
ここで、工程の複数の要素が想定外に相互作用する例を簡単に説明します。ある加工現場では切削時間 2 分、被削材の取り付け/取り外しに計 2 分を義務付けています。工具交換に 1 分、5 個の部品加工で工具が寿命に達し、工具のコーナチェンジに 1 部品あたり 0.20 分かかります。各部品の加工には 4.2 分必要なため、生産量は 1 時間あたり被削材 14 個前後となります。各工具のコストは 15 ユーロで、被削材 5 個で工具が寿命に達するため、被削材 14 個の加工には工具 2.8 個(42 ユーロ)が必要です。加工コストは 1 時間あたり 50 ユーロ、被削材 14 個の生産コストは 1 時間あたり 92 ユーロになります。
次に、生産量と生産性を高めようと、現場で切削速度を 10 %上げたとします。これにより、切削時間を 10 %(1.8 分)短縮できますが、工具寿命は約半分まで短縮されます。つまり、切れ刃 1 個で、交換までに被削材 2.5 個を加工できます。これまでと同様に、工具交換に 1 分、被削材の取り付け/取り外しに 2 分かかります。被削材 1 個の生産には 4.2 分(切削に 1.8 分、被削材の取り扱いに 2 分、工具交換に 0.4 分)、すなわち 1 時間あたり被削材 14 個を加工できます。加工コストと工具コストは同じですが、1 時間の加工に工具 5.6 個(工具コスト 84 ユーロ)が必要です。生産時間の短縮を目指したにもかかわらず、14 個の被削材の生産時間は変わらず、コストは 92 ユーロから 134 ユーロにまで上昇します。
この場合、切削速度を上げても、加工の生産性は向上しません。切削時間が変わると、この例の工具寿命や工具交換時間のように、加工工程のその他の要素に影響を与えます。そのため、現場では工程の変更による結果をすべて慎重に検討する必要があります。
隠れたコストのもう 1 つの例は、工程の各段階の実行に関わります。多くの加工現場では、チップ交換が隠れたコストの典型的な例です。チップ交換に 1 分が指定されているとしても、現場で実際に測定すると、交換に 2 分、3 分、あるいは 10 分かかっており、60 秒から 600 秒の差があります。
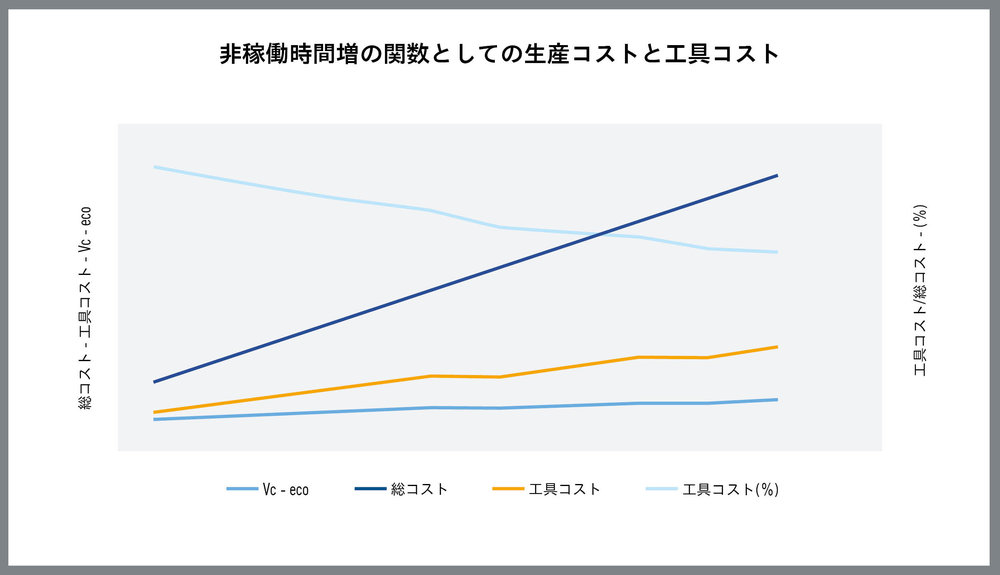
HQ ILL Production Cost And Tooling As A Function Of Increasing Idle Times.jpg
図 2
多品種少量生産の複雑な考慮事項
最近では、グローバルな競争により、製造業者は、ユーザーのニーズに応じて小ロットで様々な製品を生産するよう求めてられています。高度なコンピュータ技術により、部品の設計や加工プログラムを短時間で変更し、様々な種類の製品や在庫を容易に追跡できるようになっています。その結果、多品種少量(HMLV)生産シナリオへとシフトが進んでいます。現在までに、このアプローチは、1 桁の生産数やわずか 1 個の生産にも高い効率で対応できるまでに発展しています。
HVLM の生産計画対象期間を延長すると、工程の各要素を綿密に計画し、微調整できます。しかし、HMLV 環境の計画作成は、従来とはまったく異なります。コンピュータ化されたエンジニアリングおよびインベントリ技術により、製品の種類と生産量が短期間で変化しても対応できますが、そのために、HMLV 計画プロセスは複雑で、状況に即時に対応する必要があります。10 個の部品の注文に続き、別の部品を 2 個、5 個、1 個の注文を受ける可能性もあります。被削材種は鋼からアルミニウム、チタンまでに及び、部品形状も単純なものから複雑なものまで様々です。試験を通じて工具寿命を判定するのに十分な時間がありません。
HMLV 生産環境で工具寿命を管理するため、現場では、通常、工具寿命を控えめに予測し、安全策として、加工回ごとに新しい工具に交換し、寿命に達するよりずっと前に廃棄しています。切削時間は、全体の中の 1 要素にすぎません。HMLV 生産では、異なる被削材や材料固定具の操作、工具の交換、チップの交換に必要な時間が、実際の切削時間よりも長いことがあります。工具、加工工具、非稼働時間、直接の人件費、被削材種などの要素に隠れたコストが含まれているかもしれません。生産経済学の最新アプローチでは、工具コスト、被削材種コスト、機器コスト、生産コスト、ダウンタイム時の機器コスト、人件費、メンテナンスコストが考慮されます。
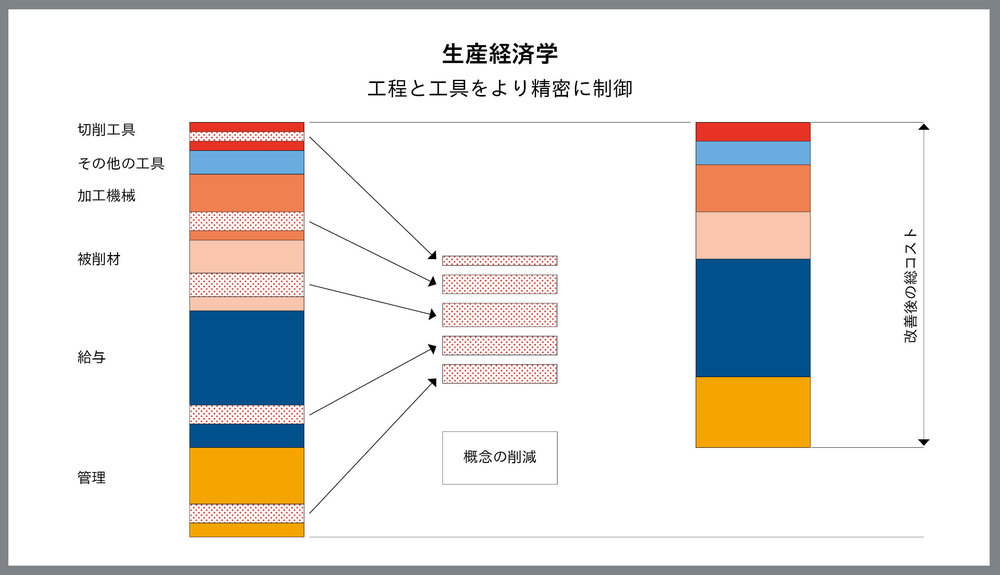
HQ ILL Production Economics
図 3
HMLV 製品の要件を急に変更すると、歩留まりを高めることは困難になります。長期にわたる HVLM 生産では、試験と調整を通じて、歩留まりを 90 %台後半まで高めることができます。一方、HMLV の歩留まりは二元的である可能性があります。1 部品で 100 %の歩留まりを達成したとしても、部品が不合格、または被削材が壊れると、歩留まりはゼロになります。品質、コスト、時間効率に対する要求は変わらないものの、初回の歩留まりが何よりも優先されます。その場合、工具の破損を防ぐことが最も重要な考慮事項となります。利点は、短時間の加工では工具の摩耗に対する懸念がほとんどないため、現場では無理のない範囲で、過酷で生産的な切削パラメータを適用できることです。
1 つの関連変数が、工具の交換に適切なタイミングを決定します。交換を待ちすぎると工具が破損し、被削材を損傷しないとしても、生産が中断されるおそれがあります。一方、工具を頻繁に交換すると、工具コストが上昇するほか、工具交換で加工を中断することによる時間の無駄によるコストが発生します。ツールを変更する適切なタイミングを決定するには、工具変更プロトコルを作成し、影響を追跡する規則を導入して、加工システム全体に対する交換の影響を検証する必要があります。
結論
金属切削システムの複数の要因は、1 対 1 で対応しているのではありません。切削条件、被削材種、または生産量を変更すると、工具寿命に影響するとともに、その他の多くの加工システムの側面に影響します。製造施設での生産経済学の課題は、要素間の関係を認識し、実践的に各要素を取り扱う戦略を策定することです。残念ながら、現場の作業員は数学の教授ではなく、要素間の関係を深く追求する時間などありません。そのため、サプライヤが工程分析と管理サービスを通じて実際の業務の全容を明らかにし(補足参照)、生産性と経済的な強みを最大限まで高める方向性を提供しています。
現場管理者から、十分に業務を遂行し、顧客の要望に応えているのに損益が出るとの嘆きが頻繁に聞こえてきます。このような問題を解決するには、現代の生産経済学に沿って、業務上、数多くの要因が存在するという現実を認識し、無視されている
隠れたコストを明らかにして、取り除くことです。これにより、製造工程の収益を最大限高めることができます。
補足
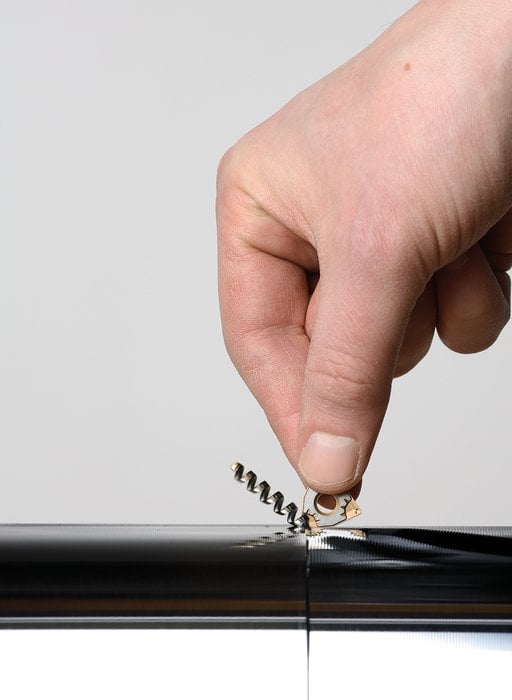
HQ IMG Duratomic Chip.jpg
図 4
自動分析
量産の初期から、製造の生産性やコストに影響を与える要因が、何倍にも増加していきます。加工作業や装置がますます複雑になるのに伴い、製造システムの要素間の関係も複雑になります。これらの要素は、単独で存在するものではありません。たとえば、生産量の要件を変更すると、工具、装置、メンテナンス、人件費などのコストに影響します。
関連する要因数と相互関係の判断は、それ自体が大きな課題です。これは非常に複雑な課題であるため、製造工程を測定、制御、管理する体系的なアプローチが必要です。
セコ・ツールズの生産性コスト分析(PCA)システムは、製造工程全体を検証して、コスト削減と生産性の向上を実現する方法を決定します。このシステムには、セコ・ツールズが世界各地で数十年にわたって蓄積した製造経験と知識が取り込まれています。セコ・ツールズはこの知識を応用して、コストモデリングを自動化するモンテカルロシミュレーション手法をはじめ、高度なコンピュータ分析とアルゴリズムを組み合わせています。
経験豊富なセコ・ツールズ担当者が PCA を実施し、工程の工具と手法をすべて評価して、工具データ、切削データ、コスト情報(部品ごとのコスト、1 時間あたりの生産量、投資コストなど)の工程の情報を盛り込んだ、包括的なレポートを作成します。PCA により、1 つの加工工具の稼働状況から、製造工場全体で被削材が移動する経路まで、工程を評価することができます。
この分析では、コストに最も大きく作用する、生産性の向上を重視しています。このシステムではボトルネックや運用上の制約を考慮して、より詳細な調査が必要な箇所を認識することができます。
初期の段階から、対象の業務または施設を対象に、時間およびコストのベンチマークから調査を実施し、PCA ソフトウェアを使って加工パラメータ、サイクルタイム、処理能力の要件などの加工要因を見直します。第 2 段階として、同じ工程で適用されている切削条件と工具を調整します。第 3 段階では、工程の変更、業務の統合、加工工具のアップグレードなどの大規模の変更の可能性を検討します。
セコ・ツールズの PCA システムを利用する製造業者は通常、業種にかかわらず、最大 30 %のコスト削減、最大 40 %の生産性向上を実現しています。
著者:
セコ・ツールズ全社技術教育マネージャ、Patrick de Vos