ABB ロボティクスがテストセンターを開設し、マテリアルハンドリングにおける3D ビジョン対応ソリューションを促進
ABB ロボティクスは、最新の3D ビジョン対応バラ積みピッキング技術を用いた自動ピック&プレースソリューションを開発するために、スウェーデンのヨンショーピングに新しいバラ積みピッキングテストセンターを開設しました。この新しいセンターは、中小企業における柔軟な自動化を促進するABBの幅広い戦略の一環です。
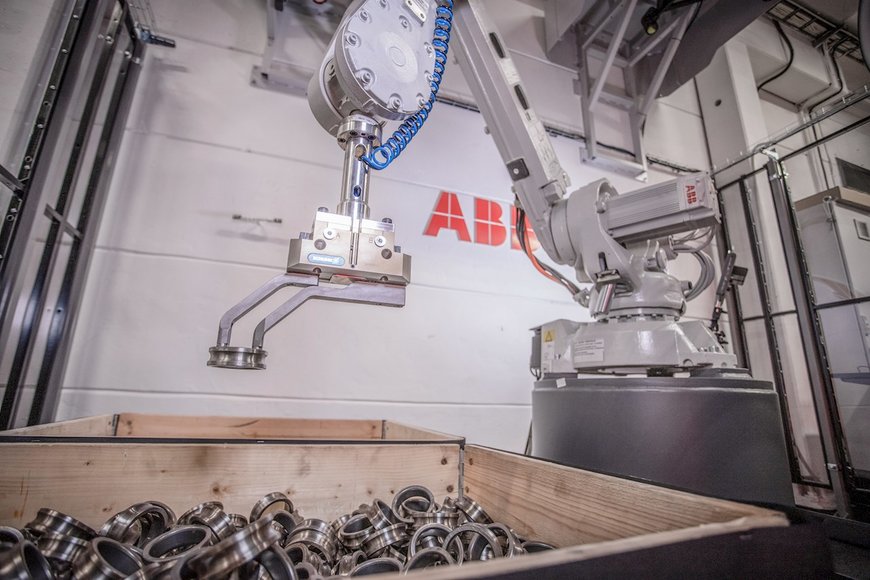
- スウェーデンのヨンショーピングに新設されたテストセンターでは、機械加工や部品供給を自動化するための3Dビジョン対応ソリューションを開発します。
- 部品処理の自動化が進むと、効率、生産性、柔軟性が向上します 。
ABBのマシンテンディング向けグローバルソリューションセンター内に設置されたテストセンターで、チームは世界中のお客さまやパートナーと革新的なソリューションを共同で開発し、自社のアプリケーションに取り入れていきます。
「新しいバラ積みピッキングテストセンターの開設は、これまで自動化が困難だった業界のプロセスの自動化を実現するための重要なマイルストーンとなります。ABBロボティクスジェネラルインダストリ ビジネスラインのマネージングディレクターであるAndrea Cassoniは、「バラバラに配置された部品を正確かつ迅速に処理することで、パーツフィーディングの柔軟性を飛躍的に向上させることができます」と述べています。「従来のシステムと比較して、当社の自動化されたばら積みピッキングソリューションは、効率的なマテリアルハンドリングにつながり、お客さまにとっては、多くの場合12ヶ月以内に大きな投資回収が可能となります」
新しいテストセンターでは、ABBのロボットと3Dビジョンを組み合わせて、規格外の構成や向きの部品を選択できるようにするばら積みピッキング技術の開発を加速させます。あらゆる方向のアイテムを認識できるため、部品をビンやパレットにバラバラに配置することができ、人手による部品の仕分けや配置の必要がありません。
従来の構造化されたばら積みピッキングシステムでは、ロボットが商品をピックアップして取り扱う前に、ワークを特定の方向に配置する必要がありました。手作業で部品を配置するのは時間がかかり、部品を繰り返し持ち上げたり供給したりすると怪我をする可能性があり、間違った位置に部品を供給するのは生産の遅れにつながります。
ばら積みピッキングを完全に自動化することで、工場のプロセスの効率性、生産性、柔軟性が向上し、マシンテンディングやパーツフィードなどのアプリケーションにおけるマテリアルハンドリングやフローが高速化されます。また、部品の入ったパレットをロボットセルに自動的に運ぶことができる自律移動ロボット(AMR)との連携など、他の工場プロセスの自動化も進むでしょう。ABBの最小のマシンテンディングセルは、フットプリントがわずか3m2なので、既存の生産ラインへの導入に新たな可能性をもたらします。
ABBの新ばら積みピッキングテストセンターでは、お客さまやパートナーが実際の環境に導入する前に、さまざまな構成やシナリオをテストすることができます。これにより、従来のばら積みピッキングアプリケーションの構築に伴うリスク、時間、コストを最小限に抑え、導入時の混乱を軽減することができます。チームは、ABBの主要なシミュレーションプログラミングツールであるRobotStudioを使用して、物理的なセルを作成する前にプロセスをモデル化し、最終的なテストと改良を行います。
ABBの自動化されたばら積みピッキングソリューションは、ABBの主要なマシンテンディング向けグローバルソリューションセンターと、3Dビジョン技術の開発と供給を専門とするパートナーのネットワークとの緊密な協力関係から生まれたものです。
www.abb.com