日立、スマート浸炭技術によるゼロエミッションギア製造のパイオニアに
日立建機とパートナー企業は、大気圧スマート浸炭技術を用いたギア製造において、日本初の直接CO₂排出ゼロを達成し、性能を維持しながら排出量とコストの削減を実現しました。
www.hitachicm.com
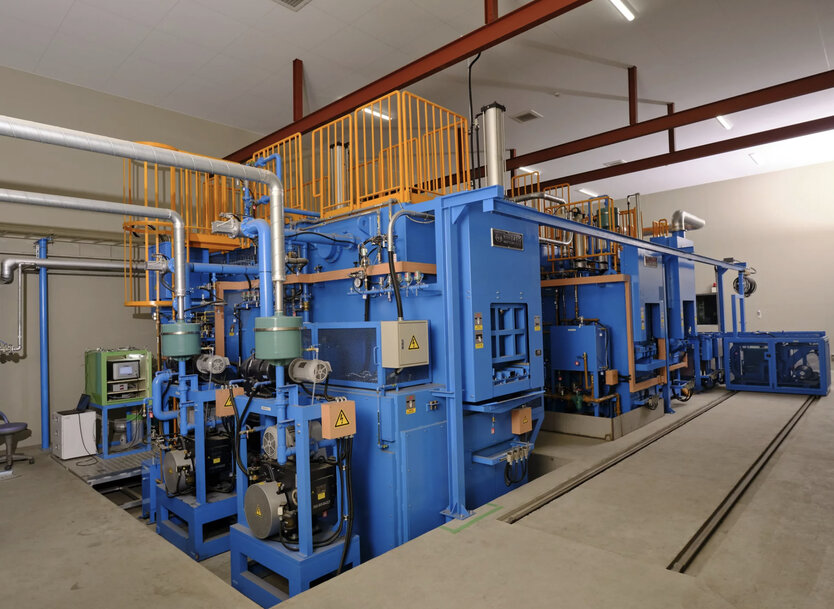
日立建機、日本テクノ、高圧ガス工業、DOWAサーモテックは、油圧ショベルの減速機に組み込まれる歯車の製造工程において、浸炭炉からの直接的なCO2排出量をゼロにできる「大気スマート浸炭技術」の有効性を国内で初めて実証しました。
浸炭とは金属の熱処理 技術の一つで、高温(約850~950℃)に加熱した低炭素の鋼材部品の表面に炭素を浸入させ、その後に急冷処理し表面を硬くする技術です。浸炭技術は耐摩耗性や疲労強度を向上させ、耐久性を高めることから、自動車や機械などに使われる部品に広く適用されています。
一般的なガス浸炭(図1)は、原料ガスである炭化水素系ガス(プロパン・メタン・ブタン)と大気から生成した変成ガス(一酸化炭素・水素・窒素)を用いて浸炭します。この方法では、浸炭反応および排ガス燃焼反応によるCO2が浸炭炉から排出されます。油圧ショベルの減速機などの機器製造工程におけるCO2排出量は、金属部品の熱処理工程が最も多く、その中でもガス浸炭は大きな割合を占めています。
日本テクノと高圧ガス工業が共同開発した本技術(図2)は、アセチレンガスと窒素ガスの流量を堀場製作所製のアセチレンガス濃度分析器により制御し、鋼材の表面に直接浸炭を行います。本技術はCO2発生の元となる変成ガスを用いないためCO2直接排出量がゼロとなり、浸炭炉1基あたり年間56tのCO2排出量を削減します。また変成炉は一般的に24時間稼働し続けるため、その分の電気代やメンテナンス費などを抑えることも可能です。さらに、既存の浸炭炉を活用できるため新たな設備導入が不要で、初期投資の低減も見込めます。
このたび4社は、20tクラスの油圧ショベルの減速機に組み込まれている歯車に対して本技術を適用し、一般的なガス浸炭と同等の耐摩耗性や疲労強度の向上を実証しました。
今後4社は、常圧スマート浸炭技術の実装に向けて開発を継続していきます。
www.hitachicm.com